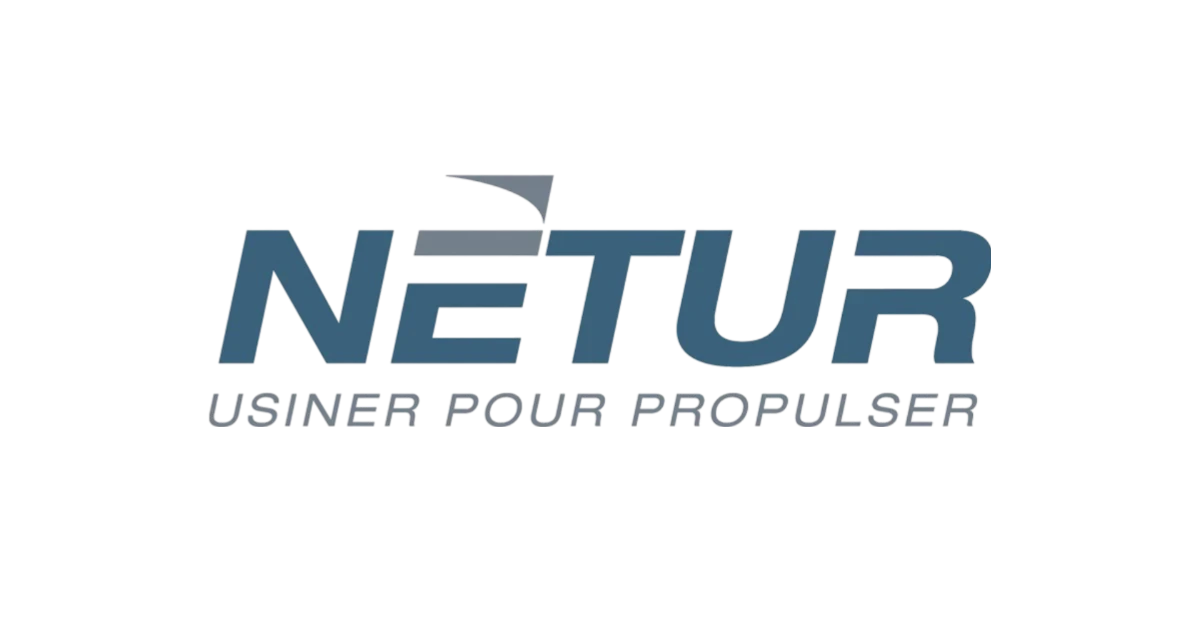
Nétur Boosts Production and Efficiency with Expert Solutions
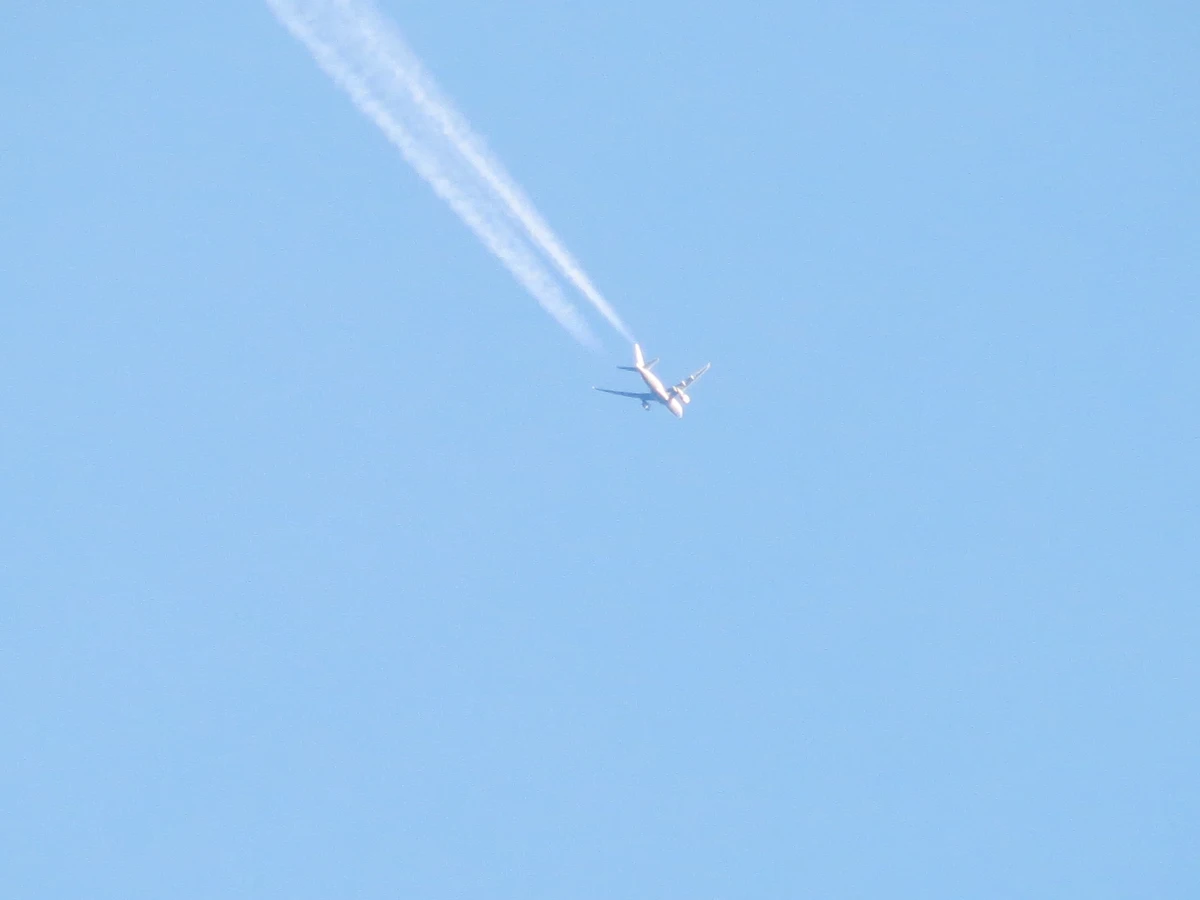
Implementation of a Daily Management System (DMS) and Lean Six Sigma Training
40% Growth in organic production
Achievement
Netur has reached some impressive results during this project, on top of the organic production growth and 10% increase in labour force. The company has established an efficient structure on the production floor, improved internal communication, was able to monitor production in real-time and establish KPIs.
"The Talan experts have provided Nétur impeccable and personalized services throughout the project. I have particularly appreciated their support following the DMS implementation, which has allowed us to feel confident while ensuring the smooth running of changes made within the company. This investment is already generating profits."
Impressive Results
- Organic production growth of 40% with a 10% increase in the labour force
- Establishment of an efficient structure on the production floor
About Nétur
Nétur has specialized in the development and machining of complex, high precision aeronautical components for more than 35 years. Based in Saint-Hubert on the south shore of Montreal, the company also offers a wide range of supplementary solutions for component assembly, painting, and special processes. Nétur’s investments in talent, ongoing skills development, and efficient processes are a guarantee of innovative, top-quality products.
Initial Situation
Nétur has recently developed a new specialty: 3D printing. This means forming metal powder into solid pieces. This futuristic project required a review of the management of manufacturing processes on the production floor.
On the other hand, as a member of the MACH initiative, launched by Aéro Montréal, Nétur wants to further stimulate continuous improvement within their company. Seeking to sustain strategic growth of the sector in the long term, the MACH initiative aims to optimize the performance of Québec's aerospace supply chain in order to increase its international competitiveness. As part of this project, an auditor comes to Nétur and identifies opportunities for improvement so that the company can access a higher level of the program.
These two main reasons lead Nétur to turn to Talan to implement a daily management system (DMS).
Challenges, Objectives and Solutions
First, Talan has made a diagnosis of Nétur’s current management system, which made it possible to target deviations from the industry’s best practices for day-to-day operations management. Using evidence that demonstrates the gaps, Nétur noted that they were struggling with a lack of communication structure, making it difficult to monitor the progress of production within the teams. As a result, staff members could not know for sure if they were meeting their daily plans. The establishment of standard meeting agendas has notably favoured better communication.
Nétur also had some shortcomings regarding its production’s planning and scheduling process. Priority management was not efficient. Thus, during the DMS implementation, the latter including the associated tools, have been optimized in order to precisely plan the production on the factory floor.
In addition, Nétur's new specialty, 3D printing, required reducing the labour force on the production line. The goal was to redefine the role of some engineers who were managing projects on the floor so they could focus more on designing and understanding the new technology for this kind of forward-thinking printing. This is only possible by establishing harmony on the production floor, thanks to a DMS!
The Implementation of a DMS
The implementation of a DMS mainly consists of a cultural change for not only all employees but the entire organization. This change is achieved through the implementation and standardization of operations management best practices. One of the goals is to validate the expected level of production and verify if there are any deviations from it. The participation of the employees is indeed an essential element so that they can see those deviations themselves, determine the associated potential cause(s) and solve the problem at the root.
In this case, the cultural change in Nétur was accomplished through:
- Employee autonomy, especially in their decision-making;
- The control over their processes;
- Indicators facilitating daily monitoring;
- Structured meetings.
Lean Six Sigma Training
To further stimulate continuous improvement, it is necessary to equip the staff, both managers and employees, so they can solve their own problems every day. For this reason, Lean Six Sigma, white, yellow, and green belt training courses were held to strengthen the implementation of the DMS. Training all staff really helps to leverage the full potential of employees and their creativity. This accelerates continuous improvement.
Lean Six Sigma Training is divided into three elements:
- Acquiring new knowledge on the best operational practices of the industry;
- Assimilating a proven problem-solving methodology;
- Putting into practice all the learned concepts in the context of a certification project.
Achieved Outcomes
Thus, by validating tasks using a standard agenda, defining and standardizing roles and responsibilities, and establishing a good organizational structure, the initial goals have been achieved, such as:
- Improved internal communication;
- Real-time production monitoring;
- Establishment of performance indicators.
It goes without saying that employees’ involvement, combined with Talan experts’ support, both during and following the implementation, were critical success factors. The main challenge was to ensure compliance with standard agendas by employees who are used to managing their production differently. Fortunately, the solid structure of a DMS promotes change management.
Why Talan?
Talan was very focused on the improvement of the production floor, which Nétur was looking for. The company was also impressed by the firm's experts' multitasking abilities, particularly by offering complementary training to what Nétur wanted to implement.